5 Maßnahmen
5.1 Allgemeines
Im Folgenden werden beispielhaft Lösungsansätze zur Feldreduzierung aufgezeigt, die an den konkreten Fall anzupassen sind. Dabei sind Kombinationen von Maßnahmen möglich.
Einige Maßnahmen können an bestehenden Zangen durch entsprechende Umrüstungen durchgeführt werden. Bei der Planung von neuen Zangen empfiehlt es sich, möglichst frühzeitig die Exposition gegenüber der magnetischen Flussdichte in die Planung mit einzubeziehen.
5.2 Technische Maßnahmen
5.2.1 Handgeführte Schweißzangen
An handgeführten Schweißzangen bestehen zwei dominierende Feldquellen, die zuführenden Kabel und die Schweißzange selbst. Die folgenden Maßnahmen zielen auf die Reduzierung der Feldemission dieser Quellen.
Feldreduzierte Kabel
Bei den Kabeln führt die Benutzung von Koaxialkabeln oder sogenannten polgleichgerichteten Kabeln zu einer deutlichen Reduzierung der magnetischen Felder gegenüber dem Einsatz von zwei parallel verlaufenden Einzelkabeln. Die zulässigen Werte werden häufig bereits an der Oberfläche des Kabels eingehalten.
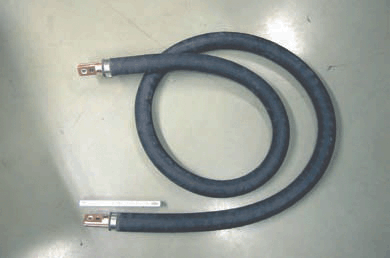
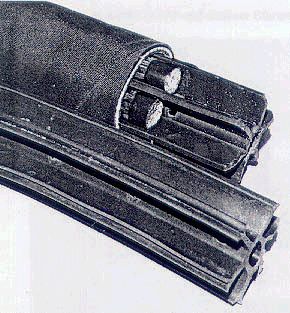
Bild 19: Polgleichgerichtetes Kabel
Allen feldreduzierten Kabeln ist gemeinsam, dass sie durch symmetrische Anordnung der Hin- und Rückleiter eine weitgehende Kompensation der auftretenden Magnetfelder erreichen. Da sich damit auch die resultierenden Kräfte aufheben, bewegt sich das Kabel bei Stromdurchfluss nicht. Aus diesem Grund wird es häufig schon aus Gründen der Haltbarkeit eingesetzt. Wie Bild 19 zeigt, ist der Knickradius trotz des mehradrigeren Aufbaus vergleichbar mit herkömmlichen Kabeln. Allerdings ist die Torsionssteifigkeit deutlich größer als bei zwei getrennten Kabeln, was sich negativ auf die Handhabbarkeit der Zange auswirkt.
Bei der Umstellung konventioneller Zangen auf koaxiale oder polgleichgerichtete Kabel müssen in der Regel die Anschlussterminals an der Zange angepasst werden.
Ersatz von Kabelzangen durch Trafozangen
Bei Trafozangen wird der hohe Sekundärstrom in der Zange erzeugt; die Anschlusskabel sind deutlich dünner als bei der Kabelzange. Je nach Bauart der Zange können die zulässigen Werte bereits an der Oberfläche der Elektrodenarme eingehalten werden. Trotz des höheren Gewichts einer Trafozange gegenüber einer Kabelzange lässt sich die Trafozange häufig leichter handhaben, weil die schweren Kabel nicht mit bewegt werden müssen und die Gewichtsausgleichshilfen („Balancer“) bezüglich des Schwerpunktes optimal platziert werden können.
Durch Griffe muss sichergestellt werden, dass der Schweißer während der Schweißung nicht mit dem Körper in den Bereich des Zangenfensters gelangen kann. Dort treten weiterhin hohe magnetische Flussdichten auf.
Handgriffe und Handhabung
„Abstand halten“ ist die einfachste und wirkungsvollste Maßnahme gegenüber hohen magnetischen Flussdichten. Bei einigen Zangen kann durch ergonomisch günstige Installation von Handgriffen sowohl die Handhabung der Zange vereinfacht, als auch die Exposition deutlich gesenkt werden. Insbesondere bei Zangen, die nur für eine geringe Anzahl von Schweißsituationen eingesetzt werden, können häufig geeignete Griffpositionen gefunden werden.
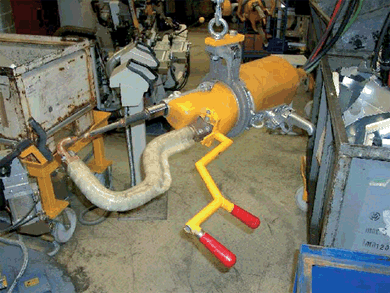
Bild 20: Trafozange mit Griffen
Änderung der Zangengeometrie
Bei kleinerem Zangenfenster ist bei gleicher Stromstärke die Feldemission in der Umgebung der Zange geringer. Daher ist eine Zange, deren Leiter möglichst lange eng beieinander sind und sich erst in der Nähe des Schweißpunktes aufspreizen, bezüglich der Feldemission günstiger einzustufen als eine rechteckige Zange (siehe auch Bild 20).
In der Regel ist die Zangengeometrie bereits auf die Schweißaufgabe optimiert, so dass nachträgliche Änderungen an bestehenden Zangen nur selten möglich sind.
Aktive Feldkompensation
Durch geeignete Maßnahmen können Felder erzeugt werden, die dem von der Schweißzange erzeugten Feld gegengerichtet sind. Das resultierende Gesamt-Magnetfeld ergibt sich durch Überlagerung beider Felder, wodurch eine Reduzierung der Exposition möglich wird.
Derartige Verfahren befinden sich noch in der Entwicklung, daher können hier keine näheren Anwendungshinweise gegeben werden.
![]() |
Reduktion der Felder am Schweißfenster durch „Gegenfeld“ |
![]() |
Erhöhung der Zangenmasse |
![]() |
Noch in der Entwicklungsphase |
5.2.2 Stationäre Schweißeinrichtungen
Bei stationären Schweißeinrichtungen ist die Schweißstromquelle in der Regel im Maschinengehäuse integriert. Aus diesem Grund wird die Feldverteilung im Wesentlichen durch die Geometrie des Schweißfensters bestimmt. Die folgenden Maßnahmen zielen daher auf die Reduzierung der Feldemission am Schweißfenster (siehe Bilder 21a und 21b).
Abschirmung
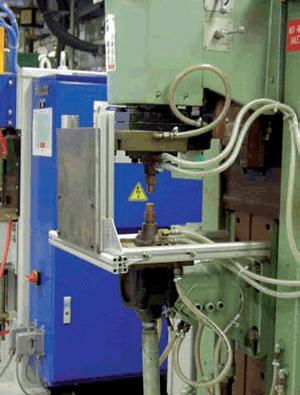
Bild 21a: Versuchsanordnung; vor dem Schweißfenster angebrachtes Schirmblech
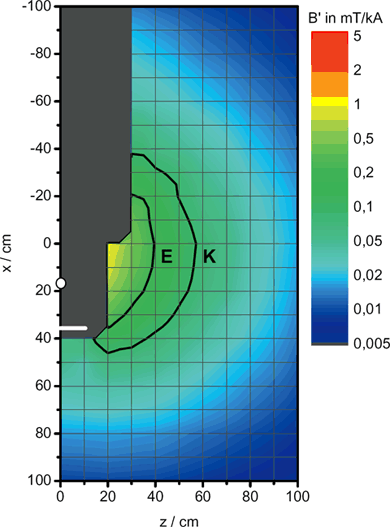
Bild 21b: Verteilung der Magnetflussdichte, Draufsicht auf horizontale Ebene durch die Mitte des Schweißfensters, eingetragene Abstandslinien für tS = 200 ms,
I = 60 kAeff (für Bereich erhöhter Exposition):
K – für Körper, E – für Extremitäten
Ausnutzung des Prinzips der Feldbeeinflussung durch Flussführung oder Wirbelstromdämpfung, meist unter Verwendung kornorientiert gewalzter Metalle.
![]() |
Abschirmung in Teilbereichen möglich |
![]() |
Materialintensiv |
![]() |
Erfordert Fachwissen bei der Konstruktion und Verarbeitung |
Änderung der Schweißfenstergeometrie
Generell gilt: Je kleiner das Zangenfenster, desto weniger Feldemission. (siehe auch Abschnitt 5.2).
Aktive Feldkompensation
Siehe Abschnitt 5.2.
5.3 Maßnahmen an der Stromquelle
Wie in Abschnitt 4.5 beschrieben, hängt die Höhe der zulässigen Werte vom Zeitverlauf des Stromes ab. Deshalb werden im Folgenden Maßnahmen an der Stromquelle zur Verringerung der Exposition vorgestellt.
Die nachfolgenden Aussagen treffen nur für Anlagenauslastungen über 30 % zu. Bei niedrigeren Auslastungen (lückender Betrieb) ist damit zu rechnen, dass sich ungünstigere Verhältnisse bei der Bewertung ergeben.
5.3.1 Ersatz von 50 Hz-Wechselstromquelle durch Gleichstromquelle
Prinzipiell bietet die Gleichstromquelle gegenüber der 50-Hz-Wechselstromquelle mehr Möglichkeiten der Signalformung (Verringerung der Flankensteilheit) und Optimierung der Schweißqualität. Der Ersatz ist jedoch nur dann sinnvoll, wenn die Restwelligkeit auf dem Gleichstrom kleiner als etwa 15 % ist.
5.3.2 Optimierung des zeitlichen Stromverlaufes
Dieses Verfahren ist nur dann anwendbar, wenn die konkrete Schweißaufgabe eine Variation von Schweißstrom und Schweißzeit zulässt.
In der Regel führt das Abflachen der Stromanstiege zu höheren zulässigen Werten.
5.4 Anlagengestaltung
Häufig verlaufen auf Grund der Anlagengestaltung die den Schweißstrom führenden Kabel (getrennter Hin- und Rückleiter) sehr nahe am Körper (Bild 22). Im Sinne der Expositionsreduzierung ist darauf zu achten, dass durch die Gestaltung der Verbindung zwischen Schweißtransformator und -zange eine starke Annäherung der Kabel an den Körper vermieden wird.
Für den Bereich Kopf und Rücken sollte ein Mindestabstand von 15 cm nicht unterschritten werden.
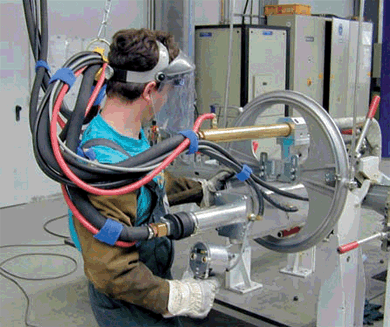
Bild 22: Beispiel für ungünstige Kabelführung
5.5 Organisatorische Maßnahmen
5.5.1 Unterweisung
In Anlehnung an die Liste aus Abschnitt 3.8 der BG-Regel „Elektromagnetische Felder“ (BGR B11) sollte die Unterweisung unter anderem folgende Inhalte aufweisen:
- Magnetfelder und Wirkungen (unmittelbar/mittelbar)
Auftreten, Charakteristik und biologische Wirkungen magnetischer Felder. Beeinflussung von aktiven Implantaten, Schutzeinrichtungen und anderen Geräten (EMV: elektromagnetische Verträglichkeit).
Elektrische Felder sind an Widerstandsschweißeinrichtungen nicht relevant. - Schutzvorschriften/Betriebsanweisungen
Erläutern von relevanten Schutzvorschriften und Betriebsanweisungen. - Schutzmaßnahmen/Sicherheitsgerechtes Verhalten
Anlagenspezifische Sicherheitsabstände, getrennt für Kopf/ Rücken, Extremitäten und für Träger von aktiven Implantaten. Für die Hand sind in vielen Fällen die zulässigen Werte für die magnetische Flussdichte bereits an der Kabeloberfläche und der Oberfläche der Elektrodenarme eingehalten.
Es gibt keine praxistauglichen persönlichen Schutzausrüstungen gegen niederfrequente Magnetfelder.
5.5.2 Kennzeichnung
Kennzeichnungen müssen von den entsprechenden Verkehrs- und Arbeitswegen deutlich wahrgenommen werden können. Sind mehrere Schweißeinrichtungen in einem Bereich vorhandenen, sollte die Kennzeichnung an den Bereichsgrenzen (Säulen oder ähnliches) angebracht werden. Die Kennzeichnung an der Schweißzange selbst ist auf Grund der mangelnden Sichtbarkeit nicht sinnvoll. Lediglich bei einzelnen stationären Schweißeinrichtungen, z.B. Buckelschweißanlagen, kann eine Kennzeichnung an der Schweißeinrichtung sinnvoll sein.
Grundsätzlich ist eine Kennzeichnung (z.B. durch Warnzeichen „Warnung vor magnetischem Feld“ nach Anhang 4 der BG-Regel „Elektromagnetische Felder“ (BGR B11), siehe auch Bild 23 in Abschnitt 5.4.4 dieser BG-Information) erst erforderlich, wenn die zulässigen Werte des Expositionsbereiches 1 überschritten sind.
Die Entscheidung, ob eine Kennzeichnung mit dem Verbotszeichen P11 „Verbot für Personen mit Herzschrittmacher“ nach der Unfallverhütungsvorschrift „Sicherheits- und Gesundheitsschutz – Kennzeichnung am Arbeitsplatz“ (BGV A8) erforderlich ist, kann nur durch eine befähigte Person anhand einer Bewertung nach Abschnitt 3.10 der Unfallverhütungsvorschrift „Elektromagnetische Felder“ (BGV B11) getroffen werden (siehe auch Abschnitt 4.4.6).
5.5.3 Zugangsbeschränkung
Die Anforderungen nach § 6 Abs. 7 der Unfallverhütungsvorschrift „Elektromagnetische Felder“ (BGV B11) können an handgeführten Schweißzangen organisatorisch umgesetzt werden, indem durch entsprechende Unterweisung des Schweißers sichergestellt wird, dass sich während des Schweißvorgangs keine Personen im Gefahrbereich der Schweißzange aufhalten.
5.5.4 Betriebsanweisung
Bild 23 zeigt eine Musterbetriebsanweisung, die an die konkrete Situation angepasst werden muss (siehe Fußnoten 1 bis 3).
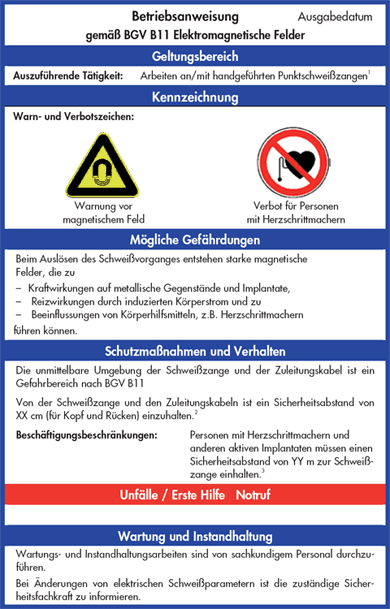
Diese Betriebsanweisung ersetzt nicht die vorgeschriebene Arbeitsplatzunterweisung.
Bild 23: Musterbetriebsanweisung für handgeführte Punktschweißzangen
Fußnoten zu Bild 23:
1) Die betreffenden Anlagen sind eindeutig, z.B. durch Typ oder Aufstellungsort zu bezeichnen. Es können auch mehrere zusammengehörende Schweißeinrichtungen als Gruppe angegeben werden. In diesem Fall müssen ggf. die Schutzmaßnahmen und Verhaltensregeln für die einzelnen Schweißeinrichtungen unterschieden werden.
2) Je nach Bauart der Widerstandsschweißeinrichtung ist die Angabe weiterer Schutzabstände notwendig. Falls erforderlich, können auch Sicherheitsabstände für Extremitäten (siehe Abschnitt 4.4.6.3) angegeben werden.
3) Hier muss der Sicherheitsabstand für Träger von aktiven Implantaten angegeben werden (siehe Abschnitt 4.4.7).
5.5.5 Veränderung der Betriebsparameter
Bei feldrelevanten Änderungen von betrieblichen Einstellungen, insbesondere die Schweißstromparameter Amplitude und Schweißzeit, aber auch die elektrischen Komponenten des Schweißstromkreises, z. B. Art und Länge der Kabel, Art oder Form der Schweißzange, sind die Bereiche erhöhter Exposition und die Gefahrbereiche neu zu bestimmen und zu dokumentieren siehe § 4 Abs. 4 und § 6 Abs. 2 der Unfallverhütungsvorschrift „Elektromagnetische Felder“ (BGV B11).
Aus diesem Grund darf der Wechsel zu einer unbewerteten betrieblichen Einstellung nicht ohne weiteres möglich sein.